The hiss of a compressor system has become everyday background noise for manufacturing facilities across the country, air consistently funneling out of systems from leaks and punctures.
With a little bit of duct tape or a tied rag, most plants are doing just enough to stay up and running. But what if it could be more efficient? What if you’re missing out on thousands of dollars because of a few simple leaks?
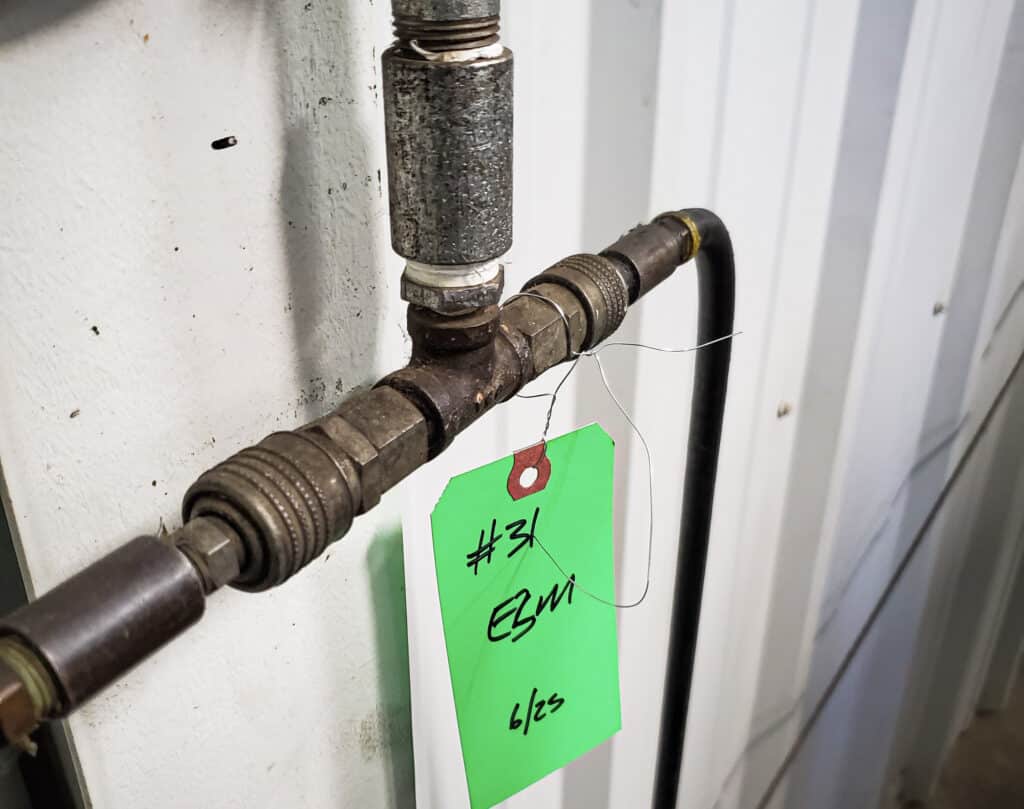
On average, 20-30% of compressed air is lost due to leaks. That means over 1/5 of the compressed air is paid for and wasted. We believe this isn’t how it should be. With the right expertise and capabilities, these leaks can easily be fixed. So, the question is where to start?
Compressed Air Systems can be complex in nature; the supply side of the system with compressors, tank(s), filters, dryers and the demand side a labyrinth of elbows, connections, regulators, fittings and hoses. Our team of Certified Energy Managers (CEM) uses supply side data loggers to monitor the run-time and performance of the system compressors. Additionally, an ultra-sonic leak detector is deployed for the demand side of the system. A full system audit’s cost is often covered up to 75% by your electric provider every 2-3 years (varies by utility) and is recommended for any system over 40 horsepower.
No matter the number, we will tag every leak and document them. From there, we build a report and plan of action to fix the leaks. For overworked maintenance teams, E3M Solutions has strategic partnerships that focus on fixing the leaks, so your team can focus on operations.
Where to begin? Right here, by connecting with E3M Solutions for a free assessment of your compressed air system. We work with your maintenance and facility staff to review the compressed air system and put together a proposed plan to audit the entire setup. Ultra-sonic leak studies should be done every 6-12 months, depending on system size, to identify the air losses between full system audits. Call us today to schedule your assessment!